TECHNOLOGY FOCUS
The computing power packed into a tiny microchip has exploded over the past several decades. A huge driver has been phenomenally successful continuous evolution in microchip fabrication equipment, materials and techniques. With each new generation of chips, as devices are scaled ever-tinier and performance requirements are ever more demanding, comes a wide range of exciting yet onerous new processing challenges, met head-on by highly motivated scientists and engineers.
The course is not geared to a particular technology node; it considers the wide range of fab processes and technology nodes in volume production today.
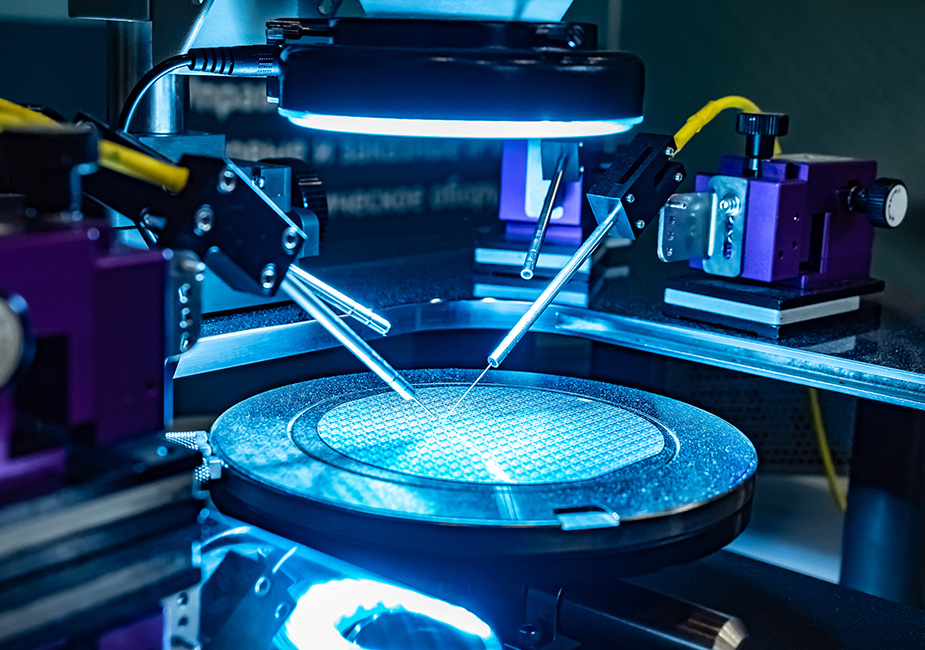
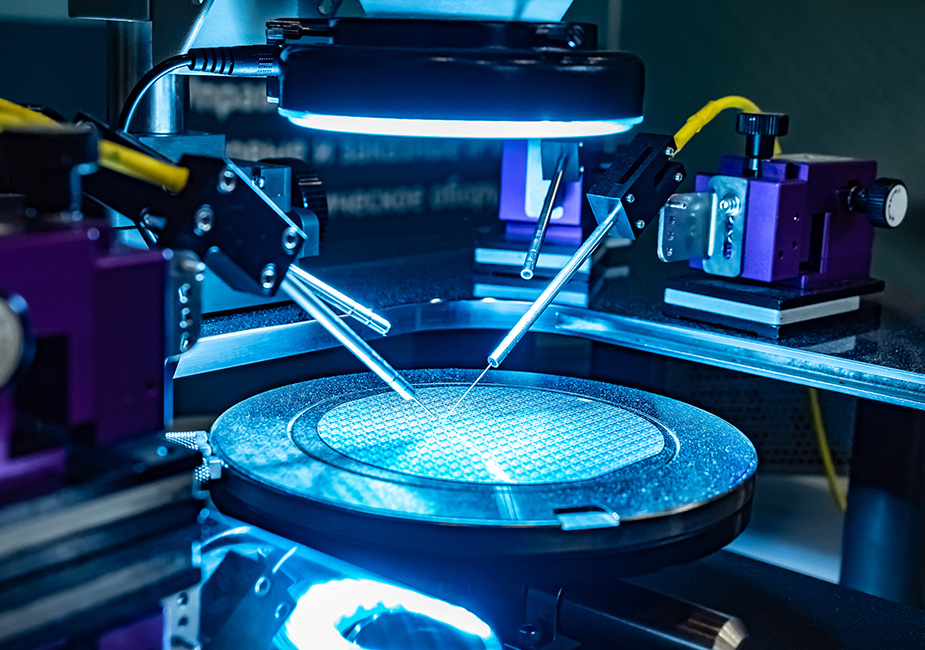
COURSE CONTENT
This 4-day course examines the entire wafer fab process, from Fab In through Parametric Test. (It also includes the details of raw Si wafer production.) Each processing technique is studied in turn. A baseline CMOS process flow is studied to introduce critical concepts of process integration. While knowledge of wafer fabrication would certainly be an asset, it is not a prerequisite. Participants will be encouraged to ask questions and to participate in brief discussions. The highly detailed course notes provided will minimize the need for note-taking during class and will serve as an excellent useful post-course reference.
WHO SHOULD ATTEND
This course is geared to a broad audience. While certainly technical in nature, it aims to also be highly practical, with a minimum of complex math and physics. Past participants have included scientists, engineers and technologists from a wide range of wafer fab equipment and materials supplier companies. Participants from wafer fabs have included process engineers, equipment engineers, yield engineers, process integration engineers, product engineers and technical managers.
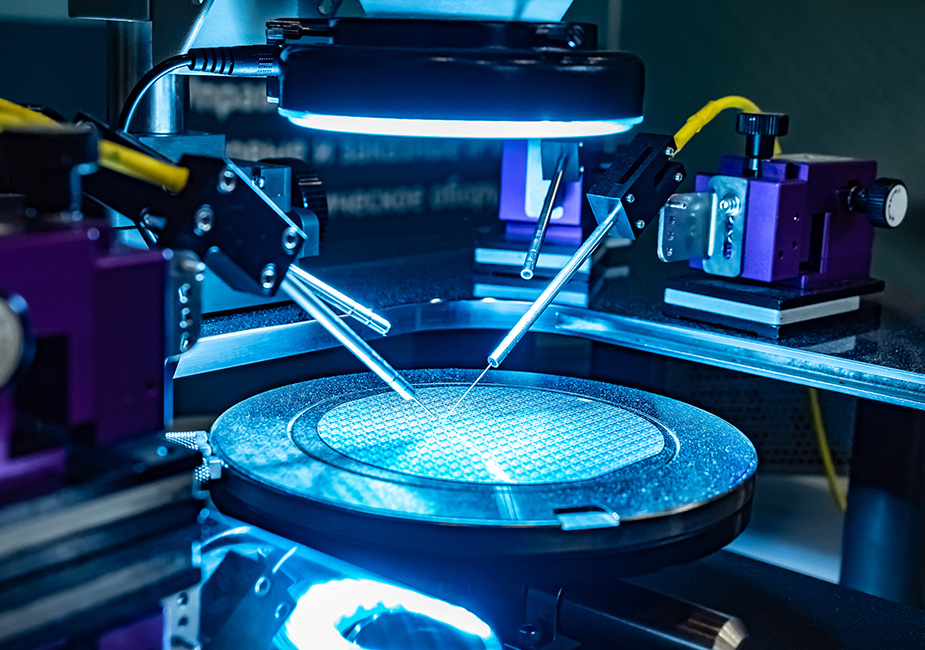
Daily Schedule
The course material is arranged into 20 modules, five per day:
Module 1: Basics and Fundamentals; Semiconductor Devices and ICs
Initialisms and Acronyms
The Language of Wafer Fab
Brief History (e.g., evolution of electronic devices and ICs; scaling)
Electrical Conductivity
Semiconductor Devices (diodes, resistors, capacitors, transistors, MOSFETs)
Common CMOS Device Problems
Classification of ICs and IC Processes
Integrated Circuit Types
The Global Semiconductor Market
Module 2: Si Crystallinity, Crystal Defects, Crystal Growth
Crystallinity
Crystal Defects
From Sand to Silicon Wafer
Controlling Crystal Defects
Module 3: Baseline CMOS Process Flow
Summary of Wafer Fab Process Techniques
Baseline CMOS Process Flow (step by step)
Process Evolution
Module 4: Doping and Ion Implantation
Doping Fundamentals
Ion Implantation Fundamentals
Dopant Profiles
Crystal Damage & Annealing
Implant Equipment
Process Challenges
Process Monitoring & Characterization
Newer Doping Techniques
Module 5: Thermal Processing
Overview of Thermal Processing
Process Applications of SiO2
Thermal Oxidation
Thermal Diffusion
Thermal Annealing
Thermal Nitridation
Process Control
Thermal Processing Equipment
Newer Process Techniques (e.g., LSA, SPE, PO)
Module 6: Contamination Monitoring and Control
Forms and Effects
Sources and Control
Characterization and Measurement
Module 7: Wafer Cleaning and Surface Preparation
Wafer Cleaning Strategies
Chemical Cleaning
Aqueous Chemical Cleaning Equipment
Mechanical Cleaning
Newer Techniques (e.g., SCCO2, MD)
Module 8: Thin Films
Definitions
Film Formation Techniques
Important Properties
Metrology
Module 9: Vacuum Fundamentals, Plasma Fundamentals
Gas-Solid/Liquid Interactions
Vacuum Pumps
Wafer Fab Vacuum Systems
Plasma Basics
DC Diode Glow-Discharge Plasma Source
RF and HD Plasma Sources
Module 10: CVD 1: Basics, LPCVD, Epitaxy
CVD Basics
LPCVD Films
LPCVD Nitride/Poly Deposition Equipment
Epi Basics
Epi Process Applications
Epi Deposition Process
Epi Deposition Equipment
Module 11: PVD
PVD (Physical Vapour Deposition) Basics
Sputter Deposition Process
PVD Equipment
Step Coverage and Contact/Via Hole Filling
Metal Film Evaluation
Electrostatic Chucks
Module 12: Lithography 1: Photoresist Processing
Basic Lithography Process
Photoresist Materials
DUV Photoresist Process Flow
Photoresist Processing Systems
Module 13: Lithography 2: Image Formation
Basic Optics
Imaging
Overview of Imaging Equipment
Actinic Illumination
Exposure Tools
Module 14: Lithography 3: Registration, Reticles, RETs
Registration
Reticles
Resolution Enhancement Techniques (RETs)
The Evolution of Optical Lithography (EUV)
Module 15: Etch
Etch Terminology
Wet Etch Chemistries and Equipment
Dry Etch Processes
Physics and Chemistry of Plasma Etching
Dry Etch Applications
Dry Etch Equipment
Module 16: CVD 2: PECVD
CVD Basics
PECVD Equipment
CVD Films
Step Coverage
Module 17: CMP
Planarization Basics
CMP Basics
CMP Processes
Process Challenges
Equipment
Process Control
Module 18: Process Evolution 1 (Bulk Metals, IMDs); Cu ECD
Process Evolution
Al-based Interconnect
The Need for Cu and low-k IMDs
Damascene Process
Cu ECD
Low-κ IMDs
Cu Integration Challenges
Next Generation Metals
Module 19: Process Evolution 2: Gate Dielectrics, Silicides, Gates
Process Evolution
Evolution of Gate & Capacitor Dielectrics
Evolution of Silicides
Evolution of Transistor Gates
Module 20: ALD, finFETs, Misc. Processing Techniques
Atomic Layer Deposition (ALD)
Silicon on Insulator (SOI) Technology
Strained Silicon
FinFETs and Other Non-traditional Transistor Designs
3-D NAND Flash Memory
Wafer Fab’s Environmental Footprint